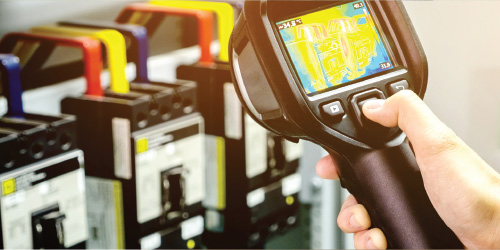
Thermographic Imaging
Failure of electrical components, wiring, and switches, causes losses totaling millions of dollars annually. Typically, many of these failures are caused by gradual deterioration, which may not be evident during visual inspection, but will be characterised by an increase in infrared radiation, or heat. Thermographic Imaging equipment can detect this increase in heat before failures occur.
It is widely accepted that planned repairs take less time to perform, and cost less, than unplanned break-down repairs. This is certainly true when it comes to fire damage resulting from electrical equipment failure. Thermographic Imaging allows the heat signatures, caused by increased electrical resistance or excessive current flow, to be seen. This allows repairs to be appropriately scheduled saving time, money and potentially avoiding catastrophic loss.
Some of the typical problems that can be detected by Thermographic Imaging include;
- Overloaded circuits
- Loose or corroded connections
- Unbalanced load
- Underspecified components
- Insulation failure
- Component failure
Thermographic Imaging is a non-invasive diagnostic procedure that should form part of your preventative maintenance program. It can assist in protecting your valuable plant and equipment, and preventing loss of income or interruption to your business, and may also safeguard your building from a destructive electrical fire.
Acerta recommends that Thermographic Imaging be conducted by a suitably qualified contractor at least once every 12 months. The equipment to be imaged will vary by location and occupation, but should at least Include all switchboards and process control panels.
Thermographic Imaging reports will provide images of each component where thermal abnormalities were identified. Generally, two images will be provided, the thermal image, and the general Image of the same component. The report will also prioritise each abnormality in terms of seriousness. For example;
Priority 1 – Serious abnormality requiring immediate attention.
Priority 2 – Not as serious, Repair as soon as possible.
Priority 3 – Abnormality noted, rectify when convenient.
Priority 4 – No abnormality noted at time of inspection, continue to monitor every 12 months.
When arranging Thermographic Imaging remember to consider the following;
- Use a suitably qualified contractor with experience in Thermographic Imaging. Ask for a sample report or check their web site.
- The Imaging should be performed when the equipment is under load, so schedule it for an appropriate time of day.
- Review the completed report with your electrical contractor to determine any corrective actions which may be required.
- Once corrective action has been taken record the details of what work was done, and the date it was completed, in the Thermographic Imaging report next to the recorded abnormality.
- Retain the report for future reference.
- Share a copy of the report with your Insurance Broker and Underwriter.
- Schedule repeat Thermographic Imaging to be reperformed within 12 months.