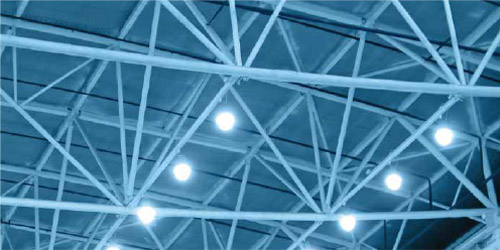
High Intensity Discharge (HID) Lighting
High Intensity Discharge (HID) lighting is commonly used in high bay factories and warehouses, and has recently been identified as the cause of a number of significant fire losses both in Australia and overseas.
A number of different types of HID lights are in use, the most common types include; Metal Halide, Mercury Vapour and Sodium Vapour. These lights utilise electrodes within a gas filled quartz or ceramic arc tube within a glass outer bulb, which operates
at very high temperatures and pressures (up to 1,300°C and 3-6 Bar of pressure). While most lights will operate for many hours without incident, a small but significant number may suffer explosive failure of the arc tube resulting in a shower
of very hot glass fragments and other material.
Explosive failures can occur as a result of physical damage or impact; escape of gases from the arc tube, thermal shock caused by contact with water, incompatible replacement parts such as ballasts and bulbs, or general aging of components caused by many
hours of use. If explosive failure occurs above or close to combustible materials, a fire may result.
Following are some helpful hints to help you avoid fires caused by HID lights:
Inspection
- Conduct a visual inspection of all installed lighting and identify the location of any HID lights.
- Ensure that HID lights are not installed directly above, or in close proximity (at least 1 metre horizontally) to where combustible materials may be stored.
- Identify any light fittings that show signs of physical damage. Immediately switch off these lights until replacement / repair can be performed by a licensed electrician.
Protection
- HID bulbs should be enclosed, including being fitted with an outer hood and containment lens (diffuser cover).
- HID bulbs should be of a type that has double shrouding to prevent the outer glass from rupturing should the arc tube explode.
- Protect lamps from water or moisture.
Maintenance
- Replacement of bulbs, and other general maintenance, should only be conducted by qualified electricians, using appropriate manufacturer specified replacement parts.
- All staff, particularly Forklift Drivers, should be advised to report any damage to light fittings immediately. Damaged lights should then be switched off until replacement / repair can be performed.
- Bulbs that switch off, then on again by themselves, need to be replaced immediately.
- Lights that are operated continuously should be cycled off for at least 15 minutes each week. Lights which flicker, take longer to come back on, or produce weaker or different coloured light should be replaced.
- Globes should be replaced when they reach 70% of rated life-span (normally expressed in hours of use).
- Consideration should be given to doing ‘Group Re-lamping’ (e.g. all the lamps in a given area are replaced at a scheduled time). This method can actually result in significant savings in labour costs and disruption to business.
Upgrades
- If contemplating a lighting upgrade, consideration should be given to LED high bay lighting, as this is not only safer, but may also provide significant savings in electricity costs.
Download your self-assessment here
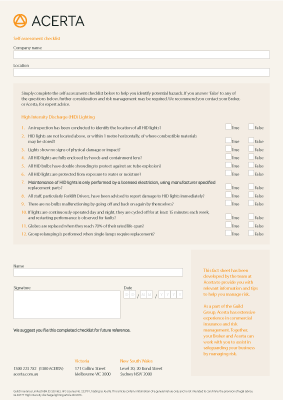